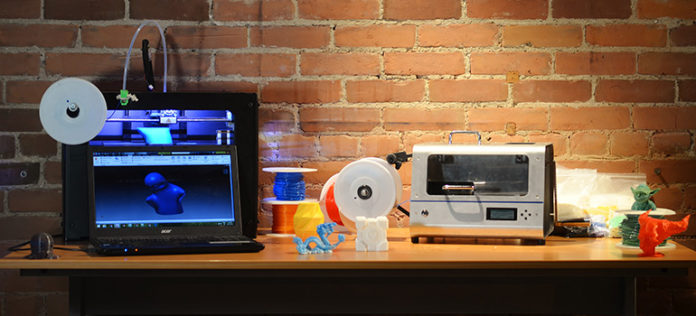
Although the idea of creating objects in three dimensions is not a new one, 3D printing or “additive manufacturing” is fairly young in the grand scheme of time. The concept and process that we are familiar with has only been around for about 40 years. Depending on your age, it may very well have been around your whole life.
The first working modern day 3D printer was created in 1984 by Charles W. Hull of 3D Systems Corp and then patented in 1987 starting yet another chapter in our “science fiction to science fact” evolution. Combining time, technological advances and curiosity, researchers and anyone who could afford these machines have tried printing anything that could be imagined. Here’s a few tidbits you may not have heard of:
1999 – Scientists manage to grow organs from patient’s cells and use a 3D printed scaffold to support them
2002 – A 3D printed miniature kidney is manufactured.
2008 – The Reprap Darwin is the first 3D printer to be able to produce many of it’s own parts
2008 – The first 3D prosthetic leg is produced
2009 – The first 3D printed blood vessel is produced by Organovo
2011 – The first 3D printed car (Urbee by Kor Ecologic)
2013 – Cody Wilson of Defense Distributed, designs the world’s first 3D printed gun
2015 – Australian researchers print the world’s first jet engine
Those are only a few of the multitude of accomplishments in what’s predicted to be a 16 billion dollar industry within the next few years.
What do they all have in common, other than a final replica product? They all need some sort of additive media, raw material…whatever you want to call it. Even though the printers themselves have drastically come down in price, from roughly $20,000 to under $1000 since 2010, the material you need is still a bit pricey. What happens when a mistake is made, a prototype is wrong or maybe your power goes out? Wasted raw materials, possibly in large and expensive amounts. This industry has the potential for unlimited good but also has the potential for massive amounts of waste, which means money out the window.
The most widely used media is plastic in filament form on a spool. For those that have never seen it, it resembles the plastic line you might use in a grass trimmer or a very thick fishing line. It comes in a multitude of colors and ranges in price from about $25 to “ouch”( or, a number so large that you would literally feel physical pain in your skull, heart and the buttock where you keep your wallet). What if you could make your own? You can with any one of the plastic filament machines available now but, most of them are slow, highly expensive and only able to make the filament from pellets… or in layman’s terms, not for free.
A few highly intelligent students at Canada’s University of British Columbia have just changed that. Welcome to the brainstorm of inventors Dennon Oosterman, Alex Kay and David Joyce’s “ProtoCycler”. This machine not only makes filament for 3d printers, it produces it faster, safer and cheaper than any other consumer available machine AND it has the ability to grind up and recycle old plastic sent to it.
ProtoCyler plugs directly into household current, is about the same size as the average 3D printer and will sell for about $700 to start. As a bonus, it can take care of your empty pop and water bottles and even recycle plastics as dense as Lego blocks!
With the growing industry of 3D printing, the growing problem of plastics being buried in the earth, and minds like these, I’d say they not only have they “hit the nail on the head”, they pounded it right through the plank and sent it into orbit! You can check out a live demo here:
Bibliography
AV Plastics. (n.d.). 3D Printing History. Retrieved 20 March 2015, from http://www.avplastics.co.uk/3d-printing-history
Students create a machine that turns used plastic into 3D printing materials. (2015). MINDS Alpha. Retrieved from https://www.minds.com/blog/view/422156424278183936/students-create-a-machine-that-turns-used-plastic-into-3d-printing-materials
UBC students launch desktop recycler that turns pop bottles into 3D printer plastic. (2015). Retrieved from http://news.ubc.ca/2015/03/05/ubc-engineering-students-develop-desktop-recycler-for-3d-printer-plastic/
Citation
(‘Students create a machine that turns used plastic into 3D printing materials’, 2015)
(‘UBC students launch desktop recycler that turns pop bottles into 3D printer plastic’, 2015)
(n.d.)